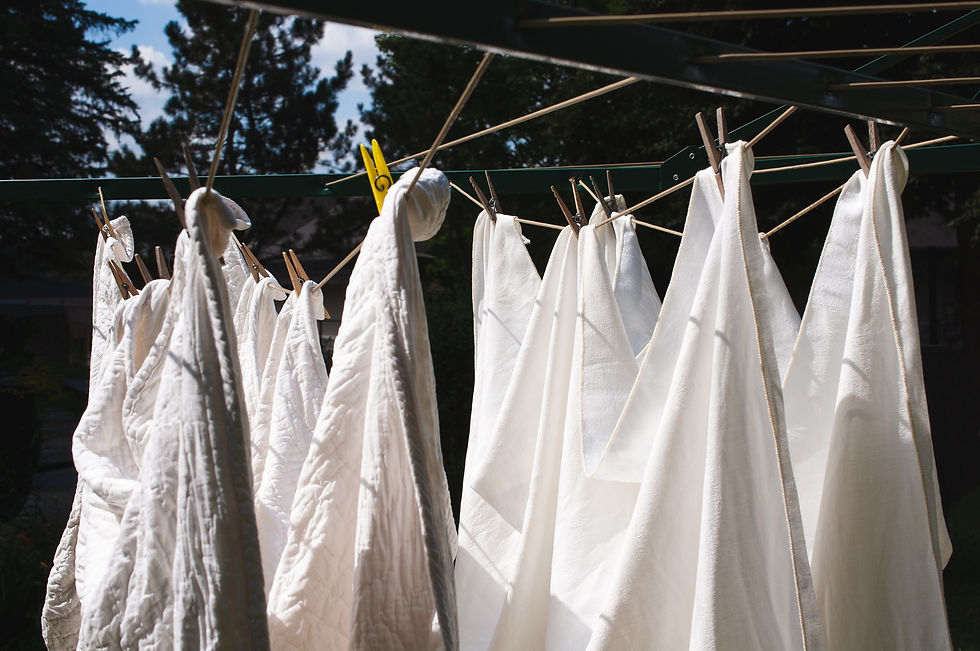
Sarah Jones
18 Apr 2023
industrial washing machine noise fix
Industrial washing machines endure rigorous cycles daily, and unusual noises often signal mechanical stress or component wear. Identifying the type of noise (banging, grinding, humming) is critical to pinpointing the root cause. Ignoring these sounds can escalate repair costs or lead to catastrophic failures. Below, we categorize common issues and their urgency levels to help you prioritize repairs and minimize downtime.
Noise Type | Likely Cause | Urgency |
Banging | Unbalanced load, loose drum | High |
Grinding | Worn bearings, foreign objects | Critical |
Squealing | Faulty belt, motor issues | Moderate |
Humming | Drain pump blockage, motor jam | Moderate |
Common Causes of Industrial Washing Machine Noise
Step-by-Step Troubleshooting Guide
1. Check for Unbalanced Loads
Industrial washers rely on balanced loads to operate smoothly. An uneven distribution of heavy linens, towels, or rugs forces the drum to shift violently during spins, creating loud banging noises. Over time, this strains the suspension system and motor mounts, accelerating wear. Addressing unbalanced loads promptly not only reduces noise but also extends the machine’s lifespan. Below, we outline quick fixes to restore equilibrium and prevent long-term damage.
Symptoms: Loud banging during spin cycles.Fix:
Stop the machine and redistribute the load evenly.
Avoid overloading (max 80% capacity).
Use smaller loads for bulky items like blankets.
Pro Tip: Opt for models with automatic load-balancing sensors (e.g., Dexter E3000) to eliminate manual adjustments.
2. Inspect the Drum Bearings
Drum bearings are the backbone of smooth rotational movement in industrial washers. When bearings wear out due to age, poor lubrication, or debris infiltration, they produce grinding or rumbling noises during cycles. Ignoring failing bearings risks seizing the drum or damaging the motor. This section guides you through diagnosing and replacing worn bearings to restore quiet operation.
Symptoms: Grinding noise from the drum area, especially during spins.Fix:
Step 1: Unplug the machine and drain water.
Step 2: Rotate the drum manually. Gritty resistance indicates worn bearings.
Step 3: Replace bearings (cost: 150–150–400 + labor).
Warning: Delayed repairs can warp the drum shaft, costing $1,000+ to replace.
3. Tighten Loose Bolts or Mounts
Vibrations from high-speed spins loosen bolts, mounts, and shock absorbers over time, leading to rattling or clanking sounds. Regular inspections ensure structural integrity and prevent components from detaching mid-cycle. Below, we detail how to secure critical parts and maintain machine stability.
Symptoms: Rattling or vibrating sounds.Fix:
Check and tighten:
Shock absorbers.
Drum mounting bolts.
Motor mounts.
Use a torque wrench to avoid over-tightening.
Real-World Example: A hotel’s Maytag washer rattled due to a loose motor mount bolt—fixed in 15 minutes.
4. Clear Foreign Objects
Coins, buttons, or screws trapped in the drum or pump can scrape against metal surfaces, causing metallic clanking. These objects often originate from improperly checked laundry loads. This section explains how to safely retrieve debris and prevent future incidents.
Symptoms: Metallic scraping or clanking.Fix:
Check pockets and seams for trapped items.
Remove the agitator or drum panel to retrieve debris.
Tool Needed: Needle-nose pliers or magnetic pickup tool.
5. Inspect the Drive Belt
The drive belt transfers power from the motor to the drum. A loose, cracked, or glazed belt slips during agitation, creating high-pitched squealing. Regular inspections prevent sudden breakdowns. Here’s how to assess belt health and ensure optimal tension.
Symptoms: Squealing during agitation.Fix:
Check for cracks, fraying, or looseness.
Replace if damaged (cost: 50–50–150).
Adjust tension to ½-inch deflection.
Brand Note: OEM belts (e.g., Speed Queen) last 5–7 years; generic belts wear faster.
6. Test the Drain Pump
A clogged drain pump strains to expel water, resulting in loud humming. Lint, coins, or fabric scraps often block the pump filter. Learn how to clear obstructions and restore proper drainage.
Symptoms: Humming with no spinning.Fix:
Clear debris from the pump filter (front/base).
Replace a clogged pump (cost: 200–200–600).
Prevention: Install lint traps and clean pumps monthly.
7. Lubricate Moving Parts
Friction from unlubricated hinges, springs, or pulleys generates squeaks. Regular greasing reduces wear and noise. Below, we recommend safe lubricants and application techniques.
Symptoms: Squeaks during cycles.Fix:
Apply food-grade silicone grease to hinges, springs, and pulleys.
Avoid petroleum-based lubes (damages rubber seals).
When to Call a Professional
While DIY fixes resolve many noise issues, certain problems demand expert intervention. Electrical failures, motor burnout, or persistent leaks pose safety hazards and require certified technicians. Below, we outline red flags that signal it’s time to call for help.
🛑 Motor failure: Burning smells or smoke.
🛑 Electrical issues: Sparks, tripped breakers.
🛑 Persistent leaks: Water pooling under the machine.
FAQs About Noisy Commercial Washers
Understanding noise-related quirks of industrial washers saves time and money. Below, we answer common questions about maintenance, costs, and preventative strategies.
Q: Can I use WD-40 on a squeaky belt?A: No—it degrades rubber. Use belt conditioner or replace it.
Q: How much does it cost to fix a noisy washer?*A: 50(DIYbeltreplacement)to50(DIYbeltreplacement)to1,500+ (motor repair).*
Q: Why does my washer shake the floor?*A: Uneven flooring or worn shock absorbers. Install anti-vibration pads (20–20–50).*
Preventative Maintenance Checklist
Proactive care minimizes noise issues and extends equipment life. Follow this checklist to keep your industrial washer running smoothly.
Daily: Check for loose items in loads.
Weekly: Clean lint filters and inspect belts.
Monthly: Lubricate hinges, tighten bolts.
Annually: Professional servicing.